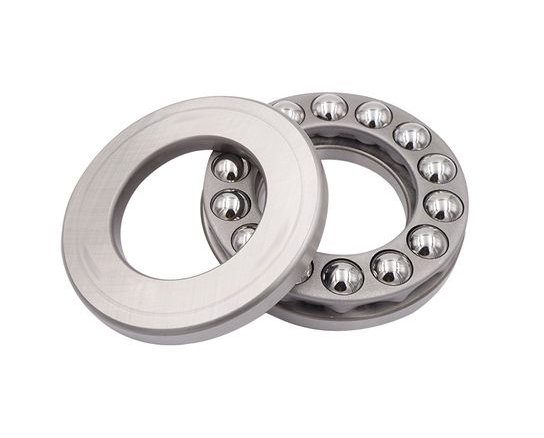
The thrust ball bearing adopts the design that can bear the thrust load during high-speed operation, and is composed of washer like ferrule with ball rolling raceway groove. Because the ferrule is cushion shaped, the thrust ball bearing is divided into two types: flat bottom cushion type and self-aligning spherical cushion type. In addition, the bearing can bear axial load, but can not bear radial load.
Composition of thrust ball bearing:
The thrust ball bearing is composed of race, shaft ring and steel ball cage assembly. The shaft ring matched with the shaft and the seat ring matched with the housing
type
According to the stress conditions, it is divided into one-way thrust ball bearing and two-way thrust ball bearing. Unidirectional thrust ball bearing can bear unidirectional axial load. Bidirectional thrust ball bearing can bear bidirectional axial load, in which the shaft ring is matched with the shaft. The bearing whose mounting surface of the race is spherical has centering performance, which can reduce the influence of installation error. The thrust ball bearing can not bear radial load and the limit speed is low.
characteristic
1. One way and two-way are available
2. In order to allow installation errors, whether unidirectional or bidirectional, you can choose spherical self-aligning spherical cushion type or spherical seat ring type.
3. High quality steel - use ultra clean steel that can prolong the service life of the bearing by up to 80%
4. High level of grease technology - NSK's lubricant technology can prolong the service life of grease and improve the performance of bearings
5. High grade steel ball - quiet and smooth when rotating at high speed
6. Use the ferrule in the option to allow installation error.
purpose
Purpose of thrust ball bearing:
It is only applicable to the parts bearing one side of axial load and low speed, such as crane hook, vertical water pump, vertical centrifuge, Jack, low-speed reducer, etc. The shaft ring, seat ring and rolling element of the bearing are separated and can be installed and disassembled separately.
assembling
There are two key points in the assembly of thrust ball bearing One is to control the pressing quality of cage and steel ball, and the other is to control the nominal height t after bearing assembly. In addition, because the shaft ring and seat ring can be separated, it brings a management problem It is to prevent mixed loading of imported bearing parts. The M-type stamping cage uses the bending edge assembly die After pressing, the steel ball is required to rotate flexibly in the pocket, but it can not fall off from the pocket. Check the movement of the steel ball in the pocket according to the technical regulations. If the solid cage is imprinted too deeply, the steel ball will have little channeling, and the connection between the embossed convex part and the cage is too few and the strength is insufficient, which is easy to fall off and cause the cage to be scrapped. There is little difference between the inner diameter of small thrust ball bearing race and shaft race, and there is no obvious difference between the two sets In order to prevent the phenomenon of mixed sleeve, it is found that both of the assembled bearings are seat rings or shaft rings. This requires certain measures to be taken Usually, when fitting, the ring drawing and seat group are distinguished with the help of auxiliary tooling, or the inner diameter plug gauge is used to check the inner diameter size before sampling the nominal height. In order to check the inner diameter conveniently, the seat ring is placed below and the shaft ring is placed above. If the inner diameter of the seat ring has obvious quenching heating oxidation color or does not go through grinding, it is not necessary to check the inner diameter size, which can clearly see the difference between the shaft ring and the seat ring and is not easy to mix. After the assembly of thrust ball bearing, the nominal height t shall be measured to confirm whether it is qualified. When measuring, calibrate with height block or standard parts and measure the load. The bearing needs to rotate dozens of times and must reach the minimum height.
When the thrust ball bearing operates at high speed, the contact angle between the steel ball and the radial plane of the raceway will be affected by centrifugal force, resulting in the sliding of the steel ball relative to the raceway. The adhesive wear caused by this sliding will damage the bearing. In order to prevent such damage, the minimum load borne by the thrust ball shaft must be guaranteed. See Formula 1 or formula 2, whichever is greater..
Formula 1: famin = k ? n * n
Formula 2: famin = COA / 1000
Famin: minimum axial load (n)
K: Minimum axial load factor
n: Speed (per minute)
CoA: basic rated static load (n)
One way thrust ball bearing can only bear the load in one direction. If it can bear the load in two directions, two-way thrust ball bearing must be selected. The minimum load or preload must be applied to the thrust ball bearing. When the shaft is vertical, the weight of the shaft usually exceeds the minimum load. At this time, due to the influence of the axial external load in the opposite direction, the acting load may be reduced.