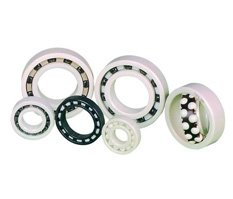
In the development and application of engineering ceramic products, ceramic ball bearing is a typical example of the wide application of engineering ceramics in the industrial field, which is highly valued by many countries. In the high-speed precision bearing, the most widely used is the hybrid ceramic ball bearing, that is, the rolling element uses hot pressed Si3N4 ceramic ball, and the bearing ring is still steel ring. The bearing has a high degree of standardization, small changes to the structure of the machine tool and is convenient for maintenance. It is especially suitable for high-speed operation. The assembled high-speed motorized spindle has the advantages of high speed, high stiffness, high power and long service life. 1. Bearing configuration: inner and outer ring bearing steel / stainless steel + ceramic ball + PA66 / stainless steel retainer + 2RS / zz2 High temperature grease
High temperature resistance
The thermal expansion coefficient of ceramic ball is small, and the bearing ball will not expand due to temperature in high temperature environment, which greatly improves the service temperature of the whole bearing. The temperature of ordinary bearing is about 160 degrees, and the temperature of ceramic ball can reach more than 220 degrees.
Ceramic ball has oil-free self-lubricating property and low friction coefficient, so ceramic ball bearing has high speed According to statistics, the speed of ceramic ball bearing is more than 1.5 times that of general bearing.
Long life
The ceramic ball can be without any grease, that is to say, even if the grease is dry, the bearing can still operate, so as to avoid the premature damage of the bearing caused by the grease in the ordinary bearing According to our test and feedback from some customers, the service life of the bearing after using ceramic ball is 2-3 times that of ordinary bearing.
insulation
The last and most important point is insulation. The bearing with ceramic ball can insulate the inner and outer rings of the bearing. Because the ceramic ball is an insulator, the insulation effect can be achieved by using ceramic ball between the inner and outer rings of the bearing This enables the bearing to be used in a conductive environment The rolling bearing is composed of ferrule, rolling element, retainer, grease and seal. When the rolling element is made of ceramic material, the rolling bearing is defined as ceramic ball bearing.
form
Because the ceramic ball itself has self-lubricating performance, it can be lubricated with or without grease according to the use requirements. The seal can also determine whether the ceramic ball bearing has a seal according to the use requirements. The retainer can also be used according to the use requirements. Then the ferrule and rolling element are two indispensable elements of the bearing. When these two elements are not made of the same material, there is the saying of hybrid construction bearing. When the rolling element is made of ceramic material, it is defined as hybrid construction ceramic ball bearing. The commonly used ceramic ball materials are zirconia (ZrO2) and silicon nitride (Si3N4); Common ferrule materials include bearing steel (GCr15), stainless iron (440, 440C) and stainless steel (304, 316, 316L).
According to the use environment, speed, load, temperature and the requirements of use, the ferrule and rolling element of ceramic ball bearing can be combined with each other by the above materials and have different use effects.
Code of ceramic ball bearing:
HY + ferrule material + bearing model + sealing type - ball material - retainer material - grease
Ferrule material: s refers to stainless iron, SS refers to stainless steel, and the specific material can be marked with registration
Dimensional stability, so as to ensure that the bearing can maintain precise size and precise fit under the working environment of temperature change, and must also have the ability of corrosion resistance and decomposition resistance under special environment. In short, the ceramic materials used to manufacture rolling bearing parts should have the following performance characteristics: 1) low density. Due to the reduction of rolling element density, its centrifugal load is also reduced during high-speed operation, Thus, it can work at higher speed. 2) medium elastic modulus. Too large elastic modulus will reduce the bearing capacity of the bushing due to stress concentration. 3) low coefficient of thermal expansion. Reduce the sensitivity to temperature changes, Make the working temperature range of the bearing wider. 4) high compressive strength. High compressive strength is the need for the rolling bearing to bear high stress. 5) high hardness and high toughness. The combination of these two characteristics can obtain better surface roughness; It can also prevent damage from external particles and impact. 6) good rolling contact fatigue resistance and spalling failure mode. 7) high temperature resistance, corrosion resistance and stability in special occasions
The contact point between the ferrule and the rolling element is subjected to the action of external load and rotation, resulting in repeated contact pressure and deformation. Due to the material performance characteristics of steel bearings, the main form of bearing failure is fatigue spalling, the fatigue life is short, and the application range is greatly limited. Ceramic materials have the advantages of low density, medium elastic modulus, small coefficient of thermal expansion, high hardness, high temperature resistance, corrosion resistance and non magnetism. Ceramic ball bearings with silicon nitride ceramic balls as rolling elements can significantly improve the contact fatigue life of bearings and greatly expand the application field of rolling bearings. They have been widely used in various high-precision and high-speed machine tools, automobiles, racing cars, subways Motor, aeroengine, petrochemical machinery, metallurgical machinery and other fields.
Silicon nitride ceramics
Ceramic bearings are widely used, but ceramic ball bearings are successfully used in the industrial field. Silicon nitride ceramic ball bearings are widely used. Their advantages are: high limit speed, good accuracy retention, small starting torque, high stiffness, good dry running performance and long service life. They are very suitable for maintaining high accuracy under high speed, high temperature, corrosion and radiation conditions For long-time operation, it is mainly used in CNC machine tools and high-speed precision machinery, such as high-speed motorized spindle bearing, machine tool spindle bearing, dental drill bearing, instrument bearing, computer hard disk drive bearing, etc. in addition, the hardness of silicon nitride ceramics is 1 times higher than that of bearing steel, and the elastic modulus is about 1 / 3 higher. Under the condition of the same load, the elastic deformation of silicon nitride ceramics is small, so, The machine tool spindle with ceramic ball bearing has good running accuracy
The hybrid ceramic bearing has been successfully applied to the spindle of high-speed machine tools and has entered the practical stage. For example, the HPM ultra precision lathe produced by Japanese companies such as Makino has a spindle speed of 16000 R / min, while the hsm700 high-speed machining center produced by American mikro company has a spindle speed of 42000 R / min and a cutting speed of 5 ~ 10 times, Hybrid ceramic bearings are also used in high speed equipment such as motorized spindle and vortex molecular pump
As an important mechanical basic part, ceramic bearing has incomparable excellent performance compared with metal bearing, high temperature resistance, super strength and so on. In recent ten years, it has been widely used in various fields of national economy and people's livelihood. Aerospace, navigation, nuclear industry, petroleum, chemical industry, light textile industry, machinery, metallurgy, electric power, food, locomotive, subway, high-speed machine tools and scientific research, national defense and military technology need to work under special working conditions such as high temperature, high speed, cryogenic, flammable, explosive, strong corrosion, vacuum, electrical insulation, non-magnetic and dry friction, and the market price of products is gradually approaching practicality, To the extent acceptable to users, the wave of large-scale application of ceramic bearings has come.
Since the 1960s, with the development and application of ceramic materials, ceramic bearings have also developed. Norton company of the United States has applied silicon nitride ceramic bearings to the hydraulic pump of the space shuttle, and the running speed of the bearings has increased by 50% ~ 100%, Ceramic bearings supplied by an American company to the American aerospace industry have been used under the high temperature of 800 * (2); Ishikawa Shimbun, a major Japanese aircraft engine manufacturer, has also tested steel ceramic hybrid bearings and all ceramic bearings on the engine
1. Low density: due to the low material density and small centrifugal load of ceramic rolling element, it can work at higher speed and produce less heat.
2. Medium elastic modulus: if the elastic modulus of ceramic rolling element is higher than that of steel rolling element, the dynamic stiffness of bearing will be improved, but the elastic modulus is too large, and the bearing capacity of bearing will be reduced due to stress concentration.
3. Small coefficient of thermal expansion: small coefficient of thermal expansion helps to reduce the sensitivity to temperature changes and prevent jamming. For hybrid roller bearings, the applicable operating speed range is wider.
4. High compressive strength: high compressive strength is the need for rolling bearings to bear high contact stress (for ceramic materials, its strength is usually determined by the fracture modulus measured by three-point or four-point bending test).
5. High hardness and high toughness: the combination of these two characteristics can obtain better surface roughness and prevent the damage of external hard particles and impact.
6. Good rolling contact fatigue resistance: this performance is very important to the requirements of bearing rolling elements.
7. Spalling failure form: if the rolling element fails in operation, it should be fatigue spalling. This effective form has an omen before jamming, which is an effective form with the least harm. In some application fields with high application conditions, ceramic materials also have some special properties.
8. High temperature resistance and stability: it can stably maintain its mechanical properties in the high temperature environment up to 800 ℃.
9. Corrosion resistance: in the oxidizing and corrosive environment, especially in the contact area where the surface oil film is squeezed out by repeated rolling, it shall have oxidation resistance and corrosion stability.
Properties of silicon nitride ceramic materials and bearing steels for industrial use
Density (kg / m3) 3250 7800 Young's modulus (GPA) 310 210 compressive strength (MPA) > 3500
Fracture modulus (MPA) 700-1000 Vickers hardness (GPA) 14-18 8 toughness (MPA · M1 / 2) 5-8 16-20
Coefficient of thermal expansion( × 10-2 / ° K) 3 12 thermal conductivity (w / MK) 20 30 specific heat (J / KGK) 800 450
Upper limit temperature (° K) 1050 400-600 high thermal shock resistance very high rolling contact fatigue failure form spalling
Classification of ceramic ball bearings
By material: ceramic bearings can be divided into zirconia ceramic bearings, silicon nitride ceramic bearings and composite ceramic bearings.
According to the structure, ceramic bearings can be divided into: zirconia ceramic bearing with retainer, silicon nitride ceramic bearing with retainer and composite ceramic bearing with retainer. Generally, the retainer material of ceramic bearing takes polytetrafluoroethylene (PTFE) as the standard configuration, and can also use glass fiber reinforced nylon 66 (grpa66-25), special engineering plastics (PEEK, PI), stainless steel (SUS316, SUS304), brass (Cu), etc. Ceramic cages are rarely used now because of difficult problems such as pocket hole processing and forming technology; Due to the material limitation of retainer, zirconia full ball all ceramic bearing without retainer, silicon nitride full ball all ceramic bearing and composite full ball ceramic bearing are developed for special applications.
According to the integrity of materials: the main components of ceramic bearings mentioned above, inner and outer rings and rolling elements are mostly made of ceramic materials, which is defined as ceramic bearings; If some of the inner and outer rings and rolling elements of the bearing are not made of ceramic materials, we define it as hybrid ceramic bearing. Ceramic ball bearings are widely used in hybrid ceramic bearings. Ceramic ball bearings are made of ceramic materials, which can be divided into zirconia ceramic ball bearings and silicon nitride ceramic ball bearings.
The problems needing attention in the use of ceramic bearings and ceramic ball bearings with different materials and structures are also different. For specific details, please consult the professional manufacturers of ceramic bearings and ceramic ball bearings for more help.
Problems in the research and development of ceramic ball bearings
First of all, what we have reported are the research and development of high-speed and high-precision ceramic ball bearings, which are usually mainly around silicon nitride balls.
The application prospect of ceramic ball bearing is prospected
Ceramic bearings and ceramic ball bearings have many excellent properties, such as self lubrication, high temperature resistance, corrosion resistance, anti magnetism, electrical insulation and so on, which need to be developed and utilized in a wider field, and the potential application field is very huge. First, high-quality high-speed ceramic ball bearing: it can well serve the domestic machine tool industry. The bearing consumption of high-speed and high-precision spindle and motorized spindle is quite large. It is estimated that the annual demand is more than several hundred thousand sets. However, the spindle bearings of high-precision machine tools require relatively high machining accuracy and harsh quality. For example, P4 bearings require high-precision ceramic balls above G5. There are few manufacturers in China and the stability of products is poor. Second: medium quality ceramic bearings can be widely and well used in petroleum exploration, crude oil smelting, especially fine chemical industry, chemical fiber, new energy, printing and dyeing, electroplating industry, sewage treatment, marine development, deep-water pump, acid-base pump, high temperature, vacuum, nuclear magnetic resonance, electrical insulation, medicine and health, X-ray tube and food industry. Many require only general accuracy levels; Medium and low speed and load; The bearing is required to be resistant to acid, alkali and salt corrosion of a certain concentration; High temperature resistance of 300 ~ 400 ℃; Non toxic and non-toxic; It can be lubricated without oil or using working medium; It can also be used in seawater. The bearings used in these fields account for a large proportion of special bearings, and ceramic bearings and ceramic ball bearings are fully capable of replacing, and can achieve the work that metal bearings are barely competent and incompetent. Engineering ceramics has its irreplaceable position. With such a huge market as the premise, we can create a new way in product development and manufacturing to broaden the greater application field of ceramic bearings. Make new materials, new processes and new technologies provide better services
First of all, what we have seen in the reports are the research and development of high-speed and high-precision ceramic ball bearings, which usually focus on silicon nitride balls. The main problems to be solved are the research on the blank making of ceramic balls and the addition of high-precision ceramic balls. In addition, the research and development of high-tech products need to go through two stages: technology intensive investment and capital intensive investment, The industrialized production of ceramic bearings not only needs to overcome many technical difficulties and use problems, but also needs large capital investment. It also needs to grasp the market positioning. People of insight in the industry need to take the development of domestic ceramic bearings and ceramic ball bearings as their own responsibility. Low price competition is bound to lead to shoddy manufacturing and further deterioration of the market. The accumulation of original capital and continuous reinvestment must serve the development of ceramic bearings and ceramic ball bearings to higher quality fields. At present, the development of ceramic bearings in China is characterized by scattered, fragmented, small-scale localized production, lack of overall consciousness and macro strategic thought.